Revolutionizing Automation: How Vision Control Systems Are Shaping the Future of Manufacturing
As the manufacturing industry continues to evolve, the demand for higher efficiency, precision, and automation is stronger than ever. In the era of Industry 4.0, the integration of smart technologies is rapidly changing how factories operate, and at the forefront of this revolution are vision control systems. These systems, often referred to as machine vision systems, are transforming traditional manufacturing processes by enabling machines to "see" and make intelligent decisions in real-time.
In this blog, we’ll explore how vision control systems are revolutionizing automation and shaping the future of manufacturing, highlighting key components, benefits, applications, and emerging trends.
What are Vision Control Systems?
Vision control systems are a form of artificial intelligence (AI)-driven technology that provides machines with the capability to perform visual inspections and tasks traditionally carried out by humans. These systems utilize cameras, sensors, and advanced image processing algorithms to capture, analyze, and interpret visual data. The insights gained are then used to guide machinery and processes, ensuring greater accuracy, speed, and reliability.
Key components of vision control systems include:
- Cameras: The eyes of the system that capture high-resolution images or videos.
- Lighting: To ensure consistent and clear imaging, proper lighting is essential in enhancing the quality of the captured data.
- Image Processing Software: This software applies algorithms to process the images and extract relevant information.
- Control Unit: The decision-making unit that interprets the processed data and sends commands to other machines or systems.
- Interfaces: Communication channels that allow the vision system to connect with robots, conveyors, or factory management systems for real-time action.
The Role of Vision Control Systems in Automation
Automation is about enhancing efficiency by minimizing human intervention. Vision control systems amplify the capabilities of automation by allowing machines to perform complex tasks such as inspection, measurement, identification, and guidance. These systems enable automated decision-making, making it possible for machines to not only execute predefined tasks but to adapt dynamically to changing circumstances in real time.
Here’s how vision control systems play a pivotal role in automation:
- Real-Time Decision Making: Machines equipped with vision systems can "see" the products or components they’re working with and make adjustments in real time. For example, a robotic arm assembling parts on a production line can detect if a component is misplaced and adjust its positioning without human intervention.
- Advanced Inspection: Quality control has traditionally relied on human inspection, but with vision systems, products can be inspected at high speed and with high accuracy. This ensures that defects are detected early, reducing waste and rework.
- Precision in Robotic Applications: Robots that are integrated with vision systems are capable of highly precise tasks, such as picking and placing objects, welding, and assembling tiny components, which are crucial in industries like electronics, automotive, and aerospace manufacturing.
Key Applications of Vision Control Systems in Manufacturing
Vision control systems have a wide range of applications in manufacturing, which are reshaping how factories operate. Some of the most impactful uses include:
1. Quality Control and Inspection
In traditional manufacturing processes, quality control relied on manual inspection, which was time-consuming and prone to human error. Vision control systems enable fully automated quality inspection, where products can be scanned at high speeds for defects such as scratches, dents, missing components, or improper alignment. For example, in pharmaceutical manufacturing, these systems can inspect pills for correct size, color, and shape, ensuring product consistency.
2. Guiding Robotic Systems
Robots used in manufacturing processes require guidance to interact with objects or materials. Vision control systems give these robots the ability to visually detect and understand the objects they are interacting with. In automotive manufacturing, for example, vision-guided robots can accurately assemble car parts by recognizing shapes and positioning components precisely.
3. Assembly Verification
Vision systems are used to verify that assembly processes are carried out correctly. They can inspect assembled products and ensure that every part is correctly placed and aligned. In electronics manufacturing, vision systems inspect circuit boards to ensure components like resistors and chips are placed correctly.
4. Dimensional Measurement and Gauging
Manufacturers often need to measure parts for dimensional accuracy. Vision control systems can perform precise measurements in real-time, ensuring that each component meets the required specifications. This is especially useful in aerospace and automotive industries, where even small measurement errors can lead to significant problems.
5. Barcode and Label Verification
In packaging and logistics, vision control systems are used to read barcodes, QR codes, and labels at high speeds. This improves the efficiency of inventory management, shipping, and tracking processes by ensuring that products are correctly labeled and coded.
Benefits of Vision Control Systems in Manufacturing
The adoption of vision control systems is transforming manufacturing in multiple ways. Here are some key benefits they offer:
1. Increased Accuracy and Precision
Vision control systems provide levels of accuracy and precision that are difficult to achieve with human operators. Whether it’s detecting minute defects in products or measuring components with high precision, these systems ensure consistent quality.
2. Enhanced Efficiency
By automating inspection and decision-making processes, vision systems enable manufacturers to increase production speed without compromising quality. Automated visual inspection is significantly faster than manual inspection, and it can operate 24/7 without fatigue.
3. Reduction in Labor Costs
Automating tasks that were traditionally done manually, such as quality control and sorting, reduces the need for human labor. This results in significant cost savings, particularly in industries with high-volume production.
4. Minimized Waste
Detecting defects early in the production process helps manufacturers minimize waste by preventing faulty products from advancing through the production line. This reduces the need for rework and material waste.
5. Improved Safety
Vision control systems reduce the need for human intervention in potentially hazardous tasks. In industries like chemical manufacturing or heavy machinery, these systems allow machines to carry out inspections in environments that could pose risks to human workers.
Emerging Trends in Vision Control Systems
As the manufacturing industry continues to advance, vision control systems are evolving to incorporate new technologies that further enhance their capabilities. Here are some of the key trends shaping the future of vision control systems:
1. Artificial Intelligence and Machine Learning
AI and machine learning are being integrated into vision systems to improve their decision-making abilities. These systems can now "learn" from previous data to recognize patterns and anomalies more effectively. This is particularly useful in predictive maintenance, where vision systems can detect early signs of machine wear and prevent breakdowns.
2. 3D Vision Systems
While traditional vision systems operate in 2D, the shift to 3D vision is enabling more complex applications. 3D vision systems provide depth information, allowing for better object recognition, even in cluttered or unstructured environments. This is revolutionizing sectors like logistics, where robots can now handle irregularly shaped packages or objects.
3. Edge Computing
Incorporating edge computing into vision control systems allows data to be processed locally, near the source of image capture. This reduces latency and enables faster decision-making, making it ideal for real-time applications in manufacturing where split-second decisions are critical.
4. Integration with IoT
Vision control systems are becoming a key part of the Industrial Internet of Things (IIoT). By connecting vision systems to other smart devices and sensors, manufacturers can create fully connected smart factories. These factories can operate autonomously, with systems continuously monitoring, analyzing, and optimizing production in real-time.
Conclusion: The Future of Manufacturing with Vision Control Systems
Vision control systems are at the heart of the next wave of innovation in manufacturing. By enabling machines to "see" and make decisions, these systems are driving greater automation, efficiency, and precision across industries. As AI, 3D imaging, and IoT integration continue to advance, vision control systems will become even more capable, opening new possibilities for smart manufacturing.
For manufacturers looking to stay competitive in the age of Industry 4.0, adopting vision control systems is no longer an option—it’s a necessity. By leveraging the power of machine vision, manufacturers can achieve new levels of productivity, quality, and innovation, ultimately shaping the future of manufacturing.
You May Also Like
These Related Stories
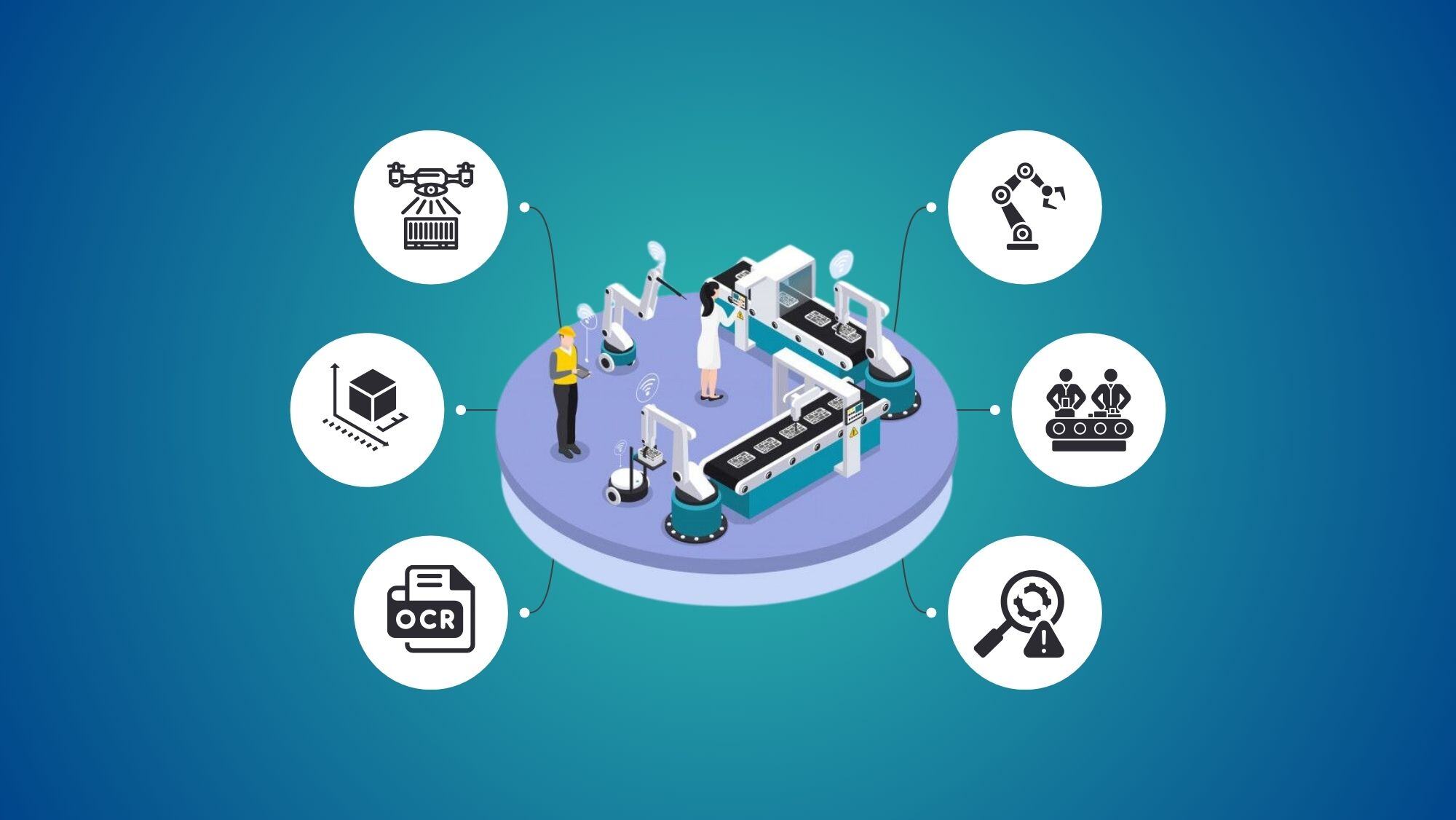
From Inspection to Automation: Top Applications of Vision Control Systems in Industry 4.0
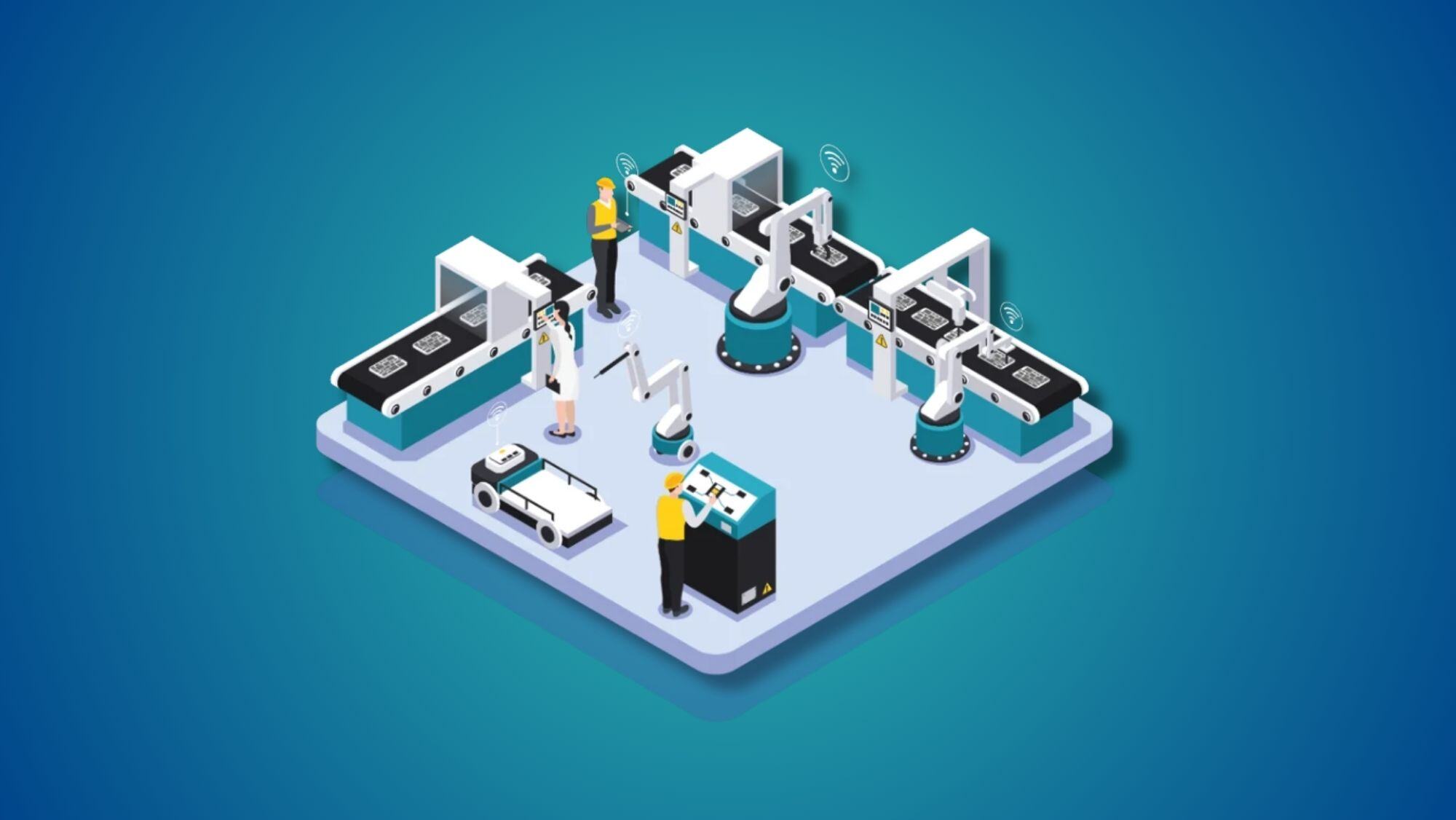
Everything You Need to Know About Vision Control Systems
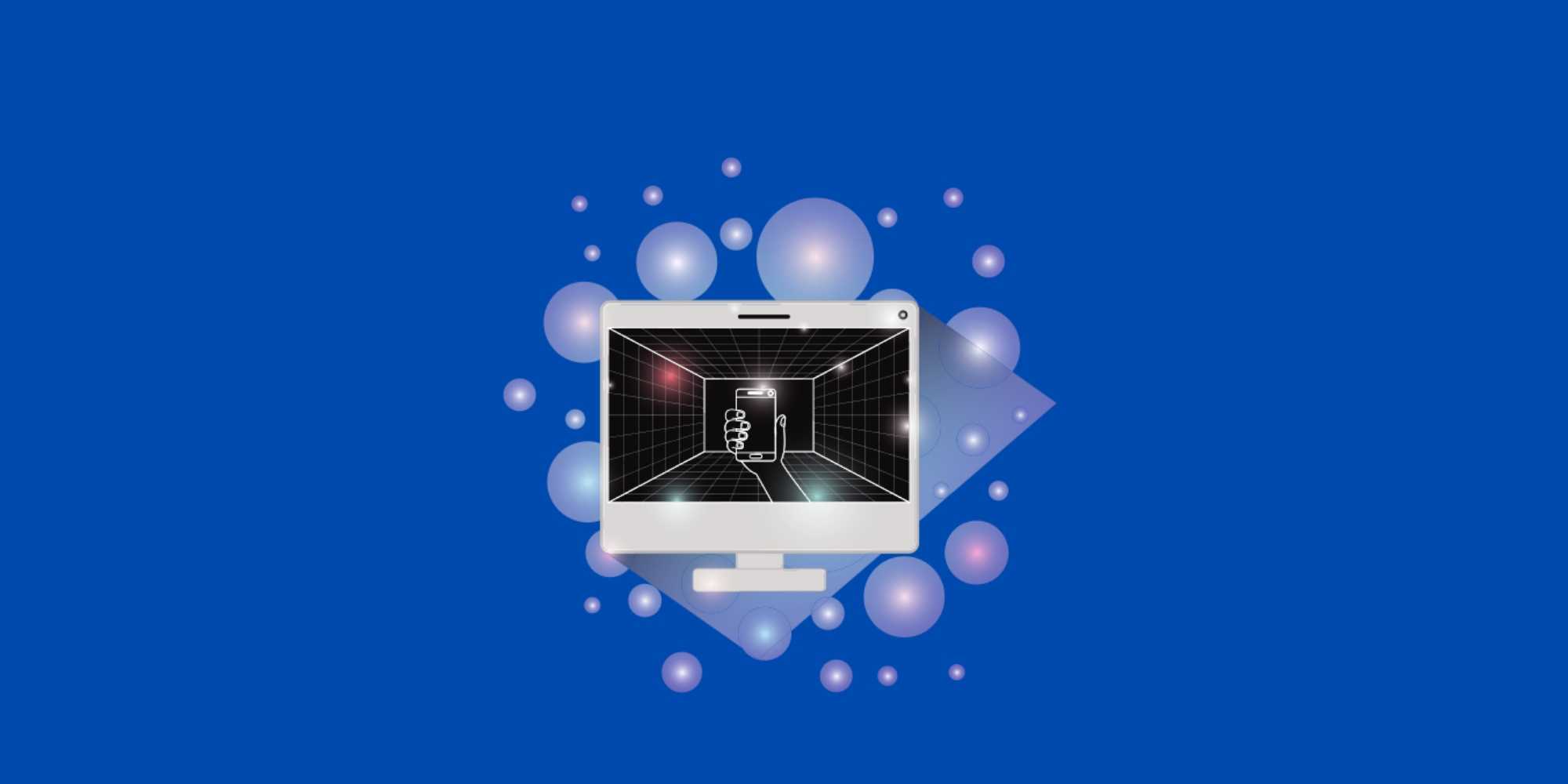
No Comments Yet
Let us know what you think